Common Mistakes When Buying Aircraft Supplies and How to Avoid Them
- Naasco .
- Feb 17
- 3 min read
When it comes to sourcing aircraft components, precision and reliability are paramount. Whether you're managing a commercial airline fleet, overseeing military aircraft maintenance, or running an FAA-approved repair station, ensuring you procure the right parts is critical to operational efficiency. However, the complexity of the aviation supply chain makes it easy to encounter pitfalls that could lead to unnecessary costs, compliance issues, or even aircraft downtime.
In this guide, we'll explore common mistakes when buying supplies from an Aircraft Supply Shop and how to avoid them.
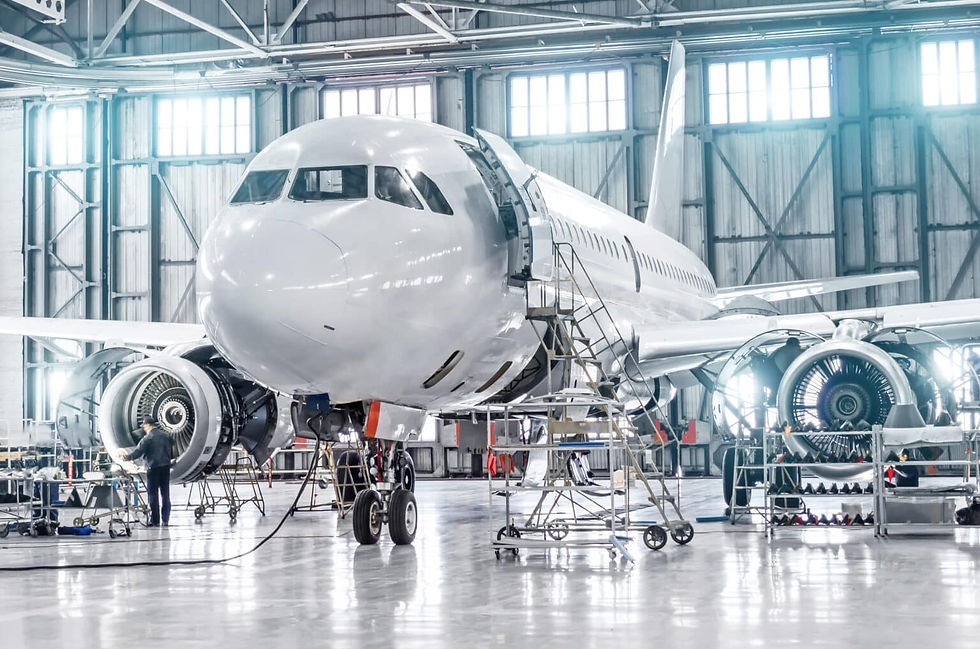
1. Failing to Source from a Trusted Supply Shop
One of the most significant mistakes buyers make is purchasing aircraft components from unverified or non-certified suppliers. The aviation industry is highly regulated, and sourcing from unreliable vendors can lead to receiving subpar or counterfeit parts, which can compromise safety and compliance.
How to Avoid It:
Always purchase from a reputable aircraft supply shop that holds necessary certifications, such as FAA approval or AS9120 certification for aerospace distributors.
Verify supplier credentials and ask for traceability documentation to ensure the parts meet aviation standards.
Work with vendors who have a strong track record in supplying quality-assured Boeing aircraft parts and Airbus helicopter parts.
2. Not Considering Lifecycle Costs Over Initial Purchase Price
Opting for the lowest-priced part might seem cost-effective in the short term, but it can lead to higher maintenance expenses, frequent replacements, and increased downtime in the long run.
How to Avoid It:
Evaluate the total cost of ownership (TCO), including repair costs, longevity, and warranty support.
Consider exchange and overhaul programs that may provide a more cost-effective solution over outright purchases.
Seek expert advice on whether a repaired or overhauled part could serve the same function as a new one while reducing costs.
3. Ignoring Compatibility and Certification Requirements
Not all parts are interchangeable, and purchasing incompatible components can lead to operational failures and non-compliance with aviation regulations.
How to Avoid It:
Always verify part numbers and specifications against manufacturer and regulatory requirements.
Ensure the supplier provides a certificate of conformity (CofC) and any required FAA 8130-3 or EASA Form 1 documentation.
Work closely with an aircraft electrical repair solutions specialist to ensure compatibility, particularly when dealing with electrical components such as aircraft blower motors.
4. Overlooking the Importance of Proper Storage and Handling
Aircraft parts, especially sensitive avionics and electrical systems require specific storage conditions to prevent degradation. Improper handling can lead to performance issues or outright failures.
How to Avoid It:
Ensure your supplier follows strict handling procedures and ships parts in protective packaging to prevent damage.
Verify that climate-sensitive components, such as aircraft blower motors, are stored in controlled environments before purchase.
Inspect shipments upon arrival and store parts according to manufacturer guidelines.
5. Delays in Ordering Critical Components
Procurement delays can result in unnecessary aircraft downtime, affecting flight schedules and maintenance operations.
How to Avoid It:
Maintain an updated inventory and anticipate lead times for critical parts like Airbus helicopter parts and Boeing aircraft parts.
Establish long-term partnerships with reliable suppliers to ensure priority access to essential components.
Consider stocking high-turnover parts to mitigate supply chain disruptions.
6. Lack of Expertise in Repair vs. Replacement Decisions
Many operators and MRO facilities struggle to determine whether a component should be repaired, overhauled, or replaced outright. Making the wrong decision can lead to unnecessary costs and extended downtime.
How to Avoid It:
Consult with experienced aircraft electrical repair solutions providers to assess the best course of action.
Take advantage of exchange programs for parts such as Boeing 777 parts, which allow for quick replacements without excessive costs.
Implement a structured evaluation process that factors in repair history, cost-benefit analysis, and expected service life.
7. Failure to Plan for Long-Term Supply Chain Stability
Relying too heavily on a single supplier or failing to diversify procurement sources can lead to disruptions if a key supplier faces shortages or regulatory issues.
How to Avoid It:
Work with multiple trusted suppliers to ensure a steady flow of essential components.
Establish agreements with vendors that provide flexible sourcing solutions, such as outright purchase, exchange, and overhaul options.
Stay informed about global supply chain trends and adjust procurement strategies accordingly.
Conclusion
Avoiding these common mistakes when purchasing aircraft supplies can significantly impact your operational efficiency, compliance, and cost-effectiveness. Partnering with a trusted aircraft supply shop ensures you receive quality components that meet stringent aviation standards. By focusing on lifecycle costs, regulatory compliance, and proactive supply chain management, you can optimize your aircraft maintenance and repair strategies for long-term success.
For high-quality aircraft blower motors, Boeing aircraft parts, Airbus helicopter parts, and expert aircraft electrical repair solutions visit NAASCO—your trusted partner in aviation MRO solutions.
Comments