Best Practices for Managing Airbus Helicopter Parts and Supplies
- Naasco .
- Apr 10
- 4 min read
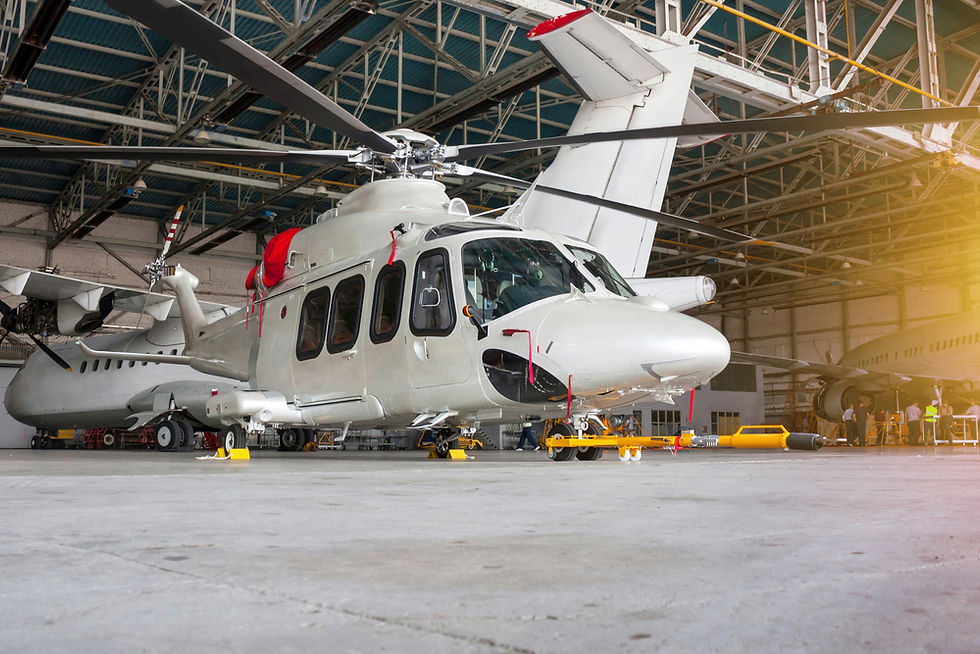
Are you looking for simple and effective ways to manage your Airbus helicopter parts and supplies? Whether you're running a busy maintenance team or just trying to stay on top of your inventory, managing helicopter parts can be challenging. But with the right practices in place, you can save time, avoid downtime, and keep your aircraft in top shape.
In this blog, here are some of the best ways to handle your parts and supplies—without overcomplicating things. Whether you're new to helicopter maintenance or a seasoned expert, these tips will help make your job easier and your operations smoother.
1. Know What You Have:
It might sound basic, but the first step in managing your Sikorsky helicopter parts is knowing exactly what you already have. Keeping an updated list of parts and supplies in your inventory can prevent unnecessary purchases and reduce waste.
Start by creating a simple inventory system that includes:
● Part Numbers
● Descriptions
● Quantities on hand
● Locations
● Expiry dates (if applicable)
This step helps you stay organized and avoid confusion during inspections or repairs.
2. Use Genuine Parts:
When it comes to helicopters, safety always comes first. Using genuine helicopter parts ensures the best performance and reliability. These parts are designed specifically for your aircraft model and meet the highest safety standards.
Non-OEM (Original Equipment Manufacturer) parts might be cheaper, but they can lead to more issues over time—costing you more in the long run. Stick with trusted, approved parts to protect both your aircraft and your crew.
3. Work with a Trusted Supplier:
Having a reliable supplier is key to getting the parts you need when you need them. Choose a supplier that:
● Has a good track record
● Offers genuine Airbus parts
● Provides clear documentation and part certifications
● Has strong customer support
A good supplier can also help you find hard-to-source parts and offer advice on alternatives if needed.
4. Keep a Minimum Stock Level:
Running out of essential parts can delay important work. That’s why it’s smart to set minimum stock levels for commonly used items. Once inventory drops below that point, it's time to reorder.
This practice often called "reorder point" management—helps keep things running without interruptions. It also avoids the panic of trying to find a part at the last minute.
5. Track Usage Trends:
Over time, you'll notice that some parts are used more often than others. By tracking which parts are replaced most frequently, you can plan better for future purchases and avoid shortages.
You can do this manually or use inventory management software to make the process smoother. Either way, keeping an eye on your trends will save you time and stress.
6. Organize Your Storage Area:
Your storage space matters more than you think. When parts are hard to find or stored incorrectly, it can lead to delays or even damage.
Use clear labels, group similar items together, and make sure everything is easy to reach. Try using storage bins, racks, and cabinets for better organization. You’ll be surprised how much more efficient things become when your storage is clean and organized.
7. Perform Regular Audits:
Even if you keep a great inventory, things can slip through the cracks. That’s why it’s helpful to do regular audits—monthly, quarterly, or yearly, depending on your needs.
Audits help you:
● Catch errors or missing items
● Remove outdated or expired parts
● Keep your inventory records accurate
A short audit now can prevent big problems later.
8. Stay Up-to-Date with Regulations:
Aviation regulations are always changing, especially when it comes to parts and maintenance. Make sure you’re aware of the latest guidelines from Airbus, the FAA, or your local aviation authority.
Following regulations keeps your aircraft airworthy and avoids fines or legal trouble. If you’re unsure about anything, ask your supplier or maintenance expert for help.
9. Train Your Team:
Your parts management system is only as strong as the people using it. Make sure your team knows:
● How to use your inventory tools
● Where parts are stored
● How to handle and label parts properly
Even short training sessions can go a long way in improving how things are run. When everyone’s on the same page, the whole process becomes faster and more efficient.
10. Plan Ahead:
Lastly, always plan for the future. If you know maintenance is coming up or certain parts are hard to find, order early. Planning ahead reduces stress and ensures your helicopters stay ready for action.
Final Thoughts:
Managing Airbus helicopter parts doesn’t have to be complicated. With a few good habits—like keeping accurate inventory, choosing quality parts, and working with trusted suppliers—you can keep everything running smoothly and safely.
Looking for a reliable partner in helicopter parts and support? Choose NAASCO. With years of experience in the aviation industry, NAASCO is known for supplying top-quality Airbus helicopter parts and helicopter Lights and offering expert support when you need it most. Contact them today and keep your fleet flying with confidence.
Comentários